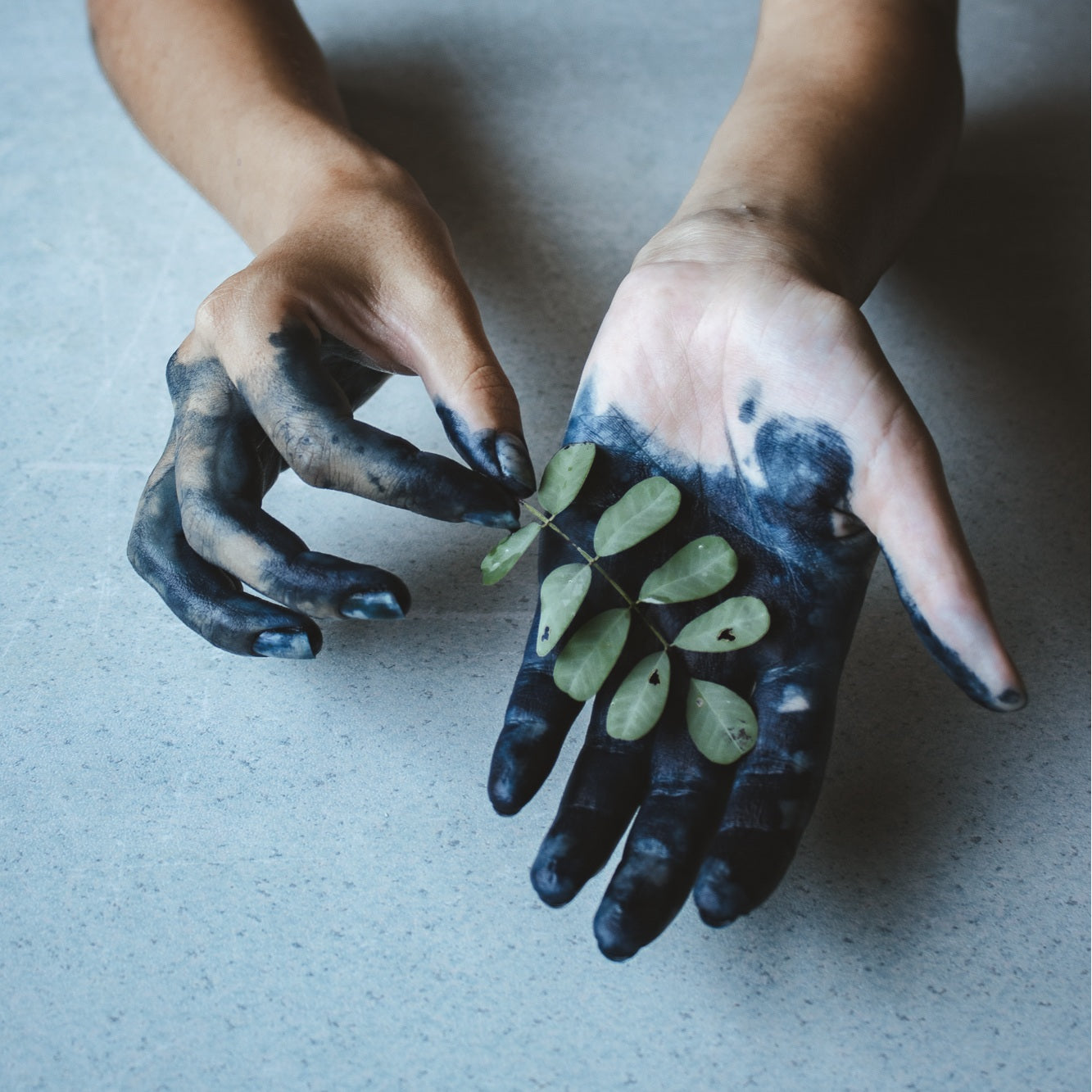
The Importance of Indigo
The indigo plant is such an important part of everything we do at Indigo Luna.
During the conception of our small brand, when experimenting with plant dyes for the first time, we fell deeply in love with the dark blue hues that could be naturally produced from such an unassuming little green plant.
We followed the process, step by step, from plant to dye to coloured garment. We learned how each stage has carefully constructed processes to minimise impact. All waste produced is 100% organic, runoff is filtered naturally through a system of plants and even the leftover mulched leaves are collected and used as compost for the next batch of new trees. Human eyes and human hands are used throughout, with all of the perfect imperfections that come with it. Leaving us with garments coloured with a deepness and uniqueness that has to be felt as well as just seen.
We left our small dye house in the jungle of Gianyar, Eastern Bali with blue stained hands and new found clarity for what path we should be taking as a brand.

The values of slow creation can be found within the story of our natural dyes. The steps needed to turn plant into colour are much slower and more costly than conventional large scale dyeing, which is well documented in its potential to poison river systems and waterways with toxic runoff.
In our plant dye gardens, each plant is grown in fields of natural entropy, where one plant is hardly distinguishable from another in beautiful chaos. Here the plants are chosen by eye, cut and then fermented over 24 hours with natural active ingredients like palm sugar and limestone.
The fermentation process leaves us with a glistening bucket of metallic blue and green that resembles a mother of pearl shell. The indigo leaves are then thanked, removed and mulched for fertiliser.
This mixture is then oxidised by scooping and pouring into another bucket over and over, until our metallic liquid has turned frothy and dark and almost ready to dye with. This step is very labour intensive and has a feeling of true magic. Thousands of years of human dyeing knowledge is channeled through Pak Nyoman smiling in a Bintang singlet, blurring the line between chemistry and alchemy.

As our mixture rests overnight, the heavy dark paste settles at the bottom. Excess water is carefully removed and this deep blue mud is filtered, stored and fermented again with palm sugar, ash water and sometimes whisky. The magic paste that is used to create our dye baths is now ready to meet fabric.
We now have our dye bath, deep blue as the surrounding oceans that lap our small island of Bali. For our underwear we are using one of the most sustainable fabrics that exists, Modal, which is material made from spinning wood pulp in a closed loop system, reusing all necessary heavy chemicals unlike most other plant based fibres. This is an amazing story for another time.
Our material can only be dyed in batches small enough to be carried by humans. These bundles are dunked, dried, checked for colour, and dunked again. Each submersion and subsequent drying results in a slightly deeper hue of blue. This process can take up to 2 - 3 weeks depending on drying times and humidity, made more difficult during the tail end of rainy season, which is when we have created the products we are describing now.
Curiously, as fabric leaves our indigo dye bath, it comes out a light green colour, before suddenly oxidising and finding its natural indigo blue right before your eyes. When we have found the hue we are looking for, the material is dried again and taken to another bath filled with heated water, vinegar, cut up banana trees and alum. This is what is used as the natural mordant to fix the colours to our Modal material.

Each batch of material is completely unique, and as carefully as we try to have consistency throughout our naturally dyed pieces, it’s ultimately impossible to make the colours exactly the same each time. Temperature, time of season, life stage of the plants, humidity and human workmanship all play a part in the eventual colour of the garment. The unique piece you are left with is the result of many natural factors and you can take solace in knowing the considered journey this garment has taken, from soil to skin, and each choice made has been to benefit those who have directly held and created them and also the planet on which we all stand upon.
Plant dyeing is not a new trend. In fact, some naturally dyed fabrics have been found in Pakistan, dating around 2500 BC. Similar dyed fabrics were found in the tombs of Egypt.
This slow, cumbersome process will never be as quick and consistently perfect as synthetic dyes, which is why this ancient practice is basically lost within the fashion industry. The textile industry, fueled by fast fashion and consumerism needs quotas, filled by cheap, consistently coloured products to be made regardless of the environmental costs.

To us, the use of plant dyes encapsulates the slow, carefully chosen values of Indigo Luna and also the changing narrative that conscious consumers, like you, are driving. Ultimately our own choices will drive change. By supporting ethical brands you are directly helping to create the world you want to see around you.
The word indigo in our name and the small leaf in our logo represent the choices that we want to always make. The importance of creating while also leaving behind the smallest footprint we can. Choose well, buy less, make it last.
Our Indigo Luna alchemist has finished creating two new Plant dyed intimate colours. She has recreated our classic Indigo and Jungle Green in strictly limited pieces. Available next week.
We hope you love them and feel the magic infused in each thread.
